How Much Does a Kiln Cost? Kiln Pricing Explained for Buyers
Ready to bring your creative visions to life with a kiln? We know that choosing the right kiln can feel like navigating a maze—especially when it comes to understanding pricing. As artists ourselves, we've been there too! That's why we've put together this friendly guide to walk you through everything that impacts kiln costs, helping you make an informed choice that's perfect for your creative journey.
What is the Cost of a Kiln? Factors to Consider...
Let's chat about what really influences kiln pricing, so you can find the perfect match for your artistic needs without any surprises along the way.
Kiln Firing Temperatures?
Understanding your kiln's maximum firing temperature is one of those "must-know" details that will make or break your creative projects. Think of it as knowing the limits of your creative canvas—it determines what kinds of materials you can work with and what effects you can achieve.
Different kilns come with different temperature capabilities tailored to specific creative needs:
A cone 6 kiln reaches about 2250°F (1232°C), perfect for many pottery projects.
Need to push the heat boundaries? A cone 10 kiln cranks it up to around 2381°F (1305°C), opening doors to more challenging projects and specialized glazes.
For those working with earthenware, there are specialized ceramic kilns designed for lower temperatures—typically around 2100°F (1150°C)—ideal for low-fire clay and glazes that create distinctive artistic results.
When you're exploring kiln options, think not only about your current projects but also where your artistic journey might take you in the future. The right temperature range gives you the creative freedom to experiment and grow your craft without limitations.
Top-Loading or Front-Loading Kiln?
The way you load your kiln might seem like a small detail, but trust us—it makes a big difference in your creative workflow! Let's explore the two main options to find what fits your studio life best.
Front-Loading Kilns:
Picture this: you've crafted a large sculpture that needs firing. With a front-loading kiln, you simply open the door and slide your creation in horizontally—no heavy lifting or awkward maneuvering required! These kilns are a dream for working with larger or heavier pieces, saving your back and making loading a breeze.
While front-loading kilns typically come with a higher price tag than their top-loading cousins, many artists find the convenience well worth the investment, especially when working with substantial creations. The design is more complex, with specialized door hinges and structural considerations that contribute to the cost difference.
Top-Loading Kilns:
Top-loading kilns feature a lid that opens upward, allowing you to place items inside from above. These kilns have earned their popularity through simplicity and user-friendliness. They're often more budget-friendly, making them a great starting point for many creative journeys.
While they might present a challenge for very large or heavy pieces (imagine leaning over to place a weighty sculpture!), they're perfect for smaller projects and studios where space efficiency matters.
Power Requirements
Electric kilns come in various models, each with unique power requirements tailored to their size and capabilities. Before purchasing a kiln, assessing whether your electrical supply can accommodate its specific power needs is imperative. This consideration is not only crucial for seamless kiln operation but also impacts the overall cost and installation process.
Kiln power requirements vary based on factors such as voltage and amperage. These specifications directly influence the price of the kiln, making it essential to align your electrical capacity with your kiln choice.
Smaller kiln models may be compatible with a standard 120V domestic wall socket, offering convenience for those with limited electrical resources. However, most kilns require a more robust power supply, typically a 240V socket similar to those used for appliances like washer-driers or stoves.
The installation of the required electrical infrastructure should not be overlooked. Collaborating with an electrician is advisable to ensure that the appropriate wiring and outlets are set up to support the kiln's power needs. While this installation incurs an extra cost, it's an essential investment to ensure the safe and efficient operation of your kiln.
Amperage is another vital consideration when assessing kiln power requirements. Kiln specifications detail the number of amps the kiln demands, which can range from 20 amps for smaller units to approximately 50 amps for larger, more powerful kilns. Kilns over 50 amps require direct wiring to the breaker box. It's crucial to verify whether your existing electrical system can accommodate these amperage requirements. Seeking guidance from an electrician is invaluable in understanding potential adaptations needed for your electrical supply.
To streamline the process and avoid unforeseen expenses, consulting with an electrician before finalizing your kiln purchase is recommended. They can assess your current electrical setup and provide insight into any adjustments or upgrades necessary to accommodate the kiln's power demands.
Heat Source
Kilns come in two main heating configurations: electrical and gas-fired. These heating methods impact not only the firing process but also the appearance of the final pottery pieces. Understanding these distinctions can guide your kiln selection and enhance your pottery creations.
Electric Kilns:
In the world of pottery, many home-based potters opt for electric kilns due to their affordability and accessibility. Electric kilns are equipped with heating elements positioned along the inner chamber's surface, generating heat for the firing process. These kilns are often preferred because of their cost-effectiveness, ease of purchase, and user-friendly operation.
Gas Kilns:
Gas-fired kilns, on the other hand, rely on either natural gas or propane to generate heat. Historically, gas kilns have been associated with higher costs, particularly when considering large, industrial-sized models. These larger gas kilns can range from approximately $7,500 for small to medium sized kilns to $65,000 for commercial units, depending on their capacity and specifications.
While it's commonly believed that gas kilns are consistently more expensive to acquire, this is not always the case. The kiln market has evolved, introducing smaller gas kiln models that are competitively priced and comparable to their electric counterparts. This development has bridged the affordability gap and expanded the accessibility of gas-fired kilns to a broader range of artists.
Advantages of Gas Kilns
One notable advantage of gas kilns is their capacity to create a reduction atmosphere during firing. Reduction refers to the deliberate reduction of available oxygen in the kiln. This atmospheric adjustment can lead to unique glaze and clay effects, resulting in pottery pieces with an earthy and organic appearance. This distinct visual character sets reduction-fired creations apart from those produced in electric kilns.
Firing pottery with a reduction atmosphere has traditionally been associated with gas kilns. The ability to replicate these effects in electric kilns has been limited. However, the availability of smaller gas kilns at competitive prices has made firing with a reduction atmosphere more attainable for artists. This evolution in kiln technology enables a broader range of potters to experiment with and explore reduction-fired pottery.
Kiln Size
The size of the kiln you choose is a big deal when it comes to pricing. Kilns can be small, handling just a few mugs, or massive, firing up a whole bunch of pieces at once.
Think about how much pottery you crank out. If it's a few pieces per week, a smaller kiln works fine. But if you're churning out a ton, you'll need a bigger kiln to fit the load. The size really slaps a tag on the price too. Take these kilns, for example. Their inner chambers can go from 0.8 to a whopping 18.5 cubic feet. That size difference shows up in the price too, ranging from around $2,000 to $8,000.
What You Want to Fire (Materials)
Various kinds of kilns serve distinct purposes in firing different materials. Whether it's pottery, glass, or even metal clay, there's a kiln tailored to the task at hand.
For instance, some kilns are versatile, and capable of firing both ceramics and glass. However, other kilns are specifically optimized for glass firing. Glass fusing kilns, designed for melding glass pieces together, tend to adopt a more compact and flat shape. This configuration suits the predominantly flat nature of glass projects. You'll often spot the heating elements on the interior roof of these kilns – these elements are essentially the metal coils responsible for generating heat.
On the flip side, electric kilns meant for pottery feature elements along the inner chamber's sidewalls, accommodating the three-dimensional structure of pottery pieces.
Apart from these distinctions, it's worth noting that glass-fusing kilns typically don't achieve the same high temperatures as ceramic kilns. This disparity arises from the lower melting point of glass compared to the maturation point of clay. As a result, glass fusing kilns are generally more budget-friendly than their ceramic counterparts. Nevertheless, it's intriguing that some glass fusing kilns can cater to small-scale, low-fire ceramic needs, such as crafting ceramic beads, jewelry, and doll heads.
Kiln Controller
Kiln controllers play a vital role in managing temperature and firing speed within kilns. These controllers come in various forms, such as units, boxes, or knobs, and hold the reins over the firing process.
The landscape of kiln controllers has witnessed significant changes over time. In earlier days, traditional kilns were manually operated through a series of dials called infinite switches that controlled the firing of the elements, defining the firing regimen. Within the realm of manual and digital control, a distinct category emerges the 'kiln sitter' kilns. These incorporate mechanical mechanisms that halt the kiln's operation upon achieving the desired temperature.
Nonetheless, the march of technology introduces a new era characterized by digital controllers, and more recently, touchscreen interfaces reminiscent of smartphones. In today's electric kiln manufacturing, digital or touchscreen controllers have become the norm. The prevalence of manual or semi-manual controllers in newly produced kilns has dwindled, while the kiln sitter's role has shifted from a primary feature to a replacement option for older models.
Interestingly, as digital advancements reshape the industry, modern kilns featuring digital or touchscreen controllers come at a higher price point, buut this has begun to flatten. This trend extends even to used kilns, where models equipped with digital interfaces tend to command higher prices compared to older models reliant on kiln sitters. Of course, the condition of the kiln remains a factor influencing these pricing dynamics.
New or Used Kiln
The price of a secondhand kiln can vary based on its age, condition, size, and power, as well as other factors we've discussed earlier. But the good news is that there are some excellent deals out there, with price ranges spanning from around $200 to $1500 or even higher. Keep an eye on online platforms like eBay, Facebook Marketplace, and Craigslist, as they frequently showcase a variety of kilns for sale.
When it comes to considering a used kiln purchase, don't skip the essential step of physically inspecting the kiln before sealing the deal. Just as you would inspect a used car, a firsthand evaluation helps you assess its condition and potential issues.
For a comprehensive guide on what to watch out for while procuring a used kiln, take a look at my detailed post on the topic.
Having a clear checklist in mind when evaluating a used kiln is vital. Skipping this step could lead to unexpected costs down the line if issues arise post-purchase. In fact, unforeseen repairs or adjustments might end up costing you as much, if not more, than what you'd spend on a new kiln.
How Much Do Kilns Cost?
Kiln prices vary widely based on type, size, features, and brand. Here's a breakdown of different kiln types and their price ranges:
1. Glass Kilns
When it comes to glass fusing kilns, you'll find a pricing spectrum that caters to different budgets. Models designed for household use, operating on a 120-volt, single-phase system, typically fall within the range of $600 to $2500.
Stepping up to the 240-volt two-phase models, however, brings a more substantial price tag. For these advanced units, anticipate a cost ranging from $1500 to $6500. Glass fusing kilns typically operate within the range of 1700 to 1800 degrees Fahrenheit. In contrast, pottery ovens can achieve temperatures of 2500 degrees Fahrenheit or even higher, showcasing a broader heat spectrum for pottery work.
Glass fusing kilns often focus on heating at a single level, unlike ceramic kilns that aim for consistent firing throughout their entire chamber. This variation in firing strategy arises from the distinct requirements of glass and ceramic processes.
For more information, here are some glass kilns that are great for your glass fusing projects:
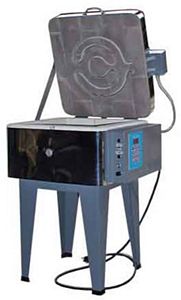
2. Ceramic Kilns
Ceramic kilns, often synonymous with the term "kiln," play a pivotal role in firing a diverse range of creations including pottery, ceramics, clay statuary, beads, and even porcelain.
Within the pottery kiln market, both electric and gas models are available. However, electric kilns enjoy a prominent position due to their superior control capabilities, especially in smaller sizes where gas-fired options are relatively scarce.
Size takes center stage when considering the price dynamics of ceramic, or pottery kilns. For smaller projects, compact electric kilns, suitable for various tasks, usually range from approximately $1000 to $2500, contingent on the model. It's worth noting that opting for a small front-loading kiln might slightly raise the price compared to top-loading alternatives. Additionally, models designed for higher-temperature firing can command a higher price point.
Here are some smaller ceramic kilns worth checking out:
Transitioning to the medium-sized category, which caters to artisans working on slightly larger pieces or needing simultaneous firing of multiple smaller creations, brings about a shift in pricing. Quality kilns in this segment typically start around the $2500 range and can extend beyond $6000.
Stepping into the realm of large-capacity pottery kilns denotes a substantial investment. These kilns are frequently found in professional studios, academic institutions, and smaller commercial settings. Within this tier, a basic model with essential features might begin around $6000 to $7000. From there, the investment can easily exceed $20,000, particularly when opting for advanced front-loading kilns.
3. Gas Kilns
Gas kilns offer a more intricate control process compared to electric kilns. Instead of simply setting a thermostat or programming cycles, regulating a gas kiln involves adjusting the gas flame and flue damper.
These types of kilns find utility in regions with limited electricity access and among experienced artists aiming for specific glaze effects achievable through gas firing. In terms of pricing, quality gas kilns typically range from $1500 to $15,000, reflecting diverse features and sizes available across models. The gas kiln path opens doors for specialized artistic endeavors, demanding precise flame management for optimal outcomes.
Here are some gas-fired kilns that you might like:
4. Electric Kilns
When in search of a reliable pottery kiln, many individuals naturally lean towards electric kilns. These kilns boast a diverse range of sizes and prices, offering ease of setup and operation. Moreover, a significant number of them are equipped with programmable controllers, allowing for an extensive selection of preset cycles.
Like any kiln purchase, several factors should be considered. However, the main decision comes down to choosing the right type of kiln the top-loading kiln or front-loading kiln.
Top-loading kilns, widely prevalent and often hailed as the most versatile can be a true asset with the right kiln furniture kit in hand. They accommodate kilns of virtually any size, plus they hold the financial advantage of being more cost-effective compared to front-loading kilns.
Nevertheless, these kilns have a drawback. Reaching into the firing chamber necessitates leaning over the kiln's sides. This can prove burdensome for those of shorter stature or those contending with back problems.
Top-loading kilns present themselves at prices as low as $1000. From there, costs can ascend significantly based on factors such as size, controller capabilities, and supplementary accessories.
Front-loading kilns offer a distinct advantage in terms of easy access to the firing chamber. With a simple opening of the door, you can insert your pottery pieces or retrieve your finished artwork.
However, these kilns come with notable downsides. You must allocate space for the door to swing open, and they do come with a higher price tag compared to top-loading alternatives.
For smaller stackable front-loading kilns, the price point is around $1500. As you venture further, the costs rise considerably, potentially reaching $15,000 or more.
If you're looking for an electric kiln, try starting here with these options:
- Olympic Kiln 2327HE
- Paragon Kiln Iguana
- Cress Kilns FX2418F
- Paragon Kiln Caldera Digital
- Evenheat Heat Treat Oven LB 27
- Hot Shot Oven and Kiln HS24-PRO Clamshell
Olympic Kiln 2327HE
5. Multipurpose Kilns
Versatile kilns are designed with smaller creative ventures in mind, spanning glasswork and PMC clay projects. They've also gained traction among knife smiths for tasks like hardening and tempering.
Most of these kilns run smoothly on standard 120-volt single-phase circuits, making them convenient for home use without requiring special wiring or extra breakers. If this is what you're looking for, then we recommend researching at-home kilns that fit your creative needs.
While some multipurpose kilns can accommodate low-fire clay, it's not a universal feature. So, it's smart to give the specs a good once-over before making a purchase.
When it comes to pricing, new multipurpose kilns usually start a little over a thousand dollars, and you'll be hard-pressed to find one exceeding the $ 3,000 mark.
So, whether you're into glass crafting, PMC clay, or even knife smithing, these versatile kilns bring flexibility to your creative playground without putting a dent in your wallet.
6. Raku Kilns
Raku kilns stand apart from the rest with their unique firing approach. With raku firing, instead of putting items into the kiln, the firing chamber is brought down over the work to be fired. This method holds deep traditional roots and is commonly used for firing stoneware, earthenware, and even ceramics.
While it's quite unlikely that most of us will have a pressing need for a Raku kiln, it's good to know that if the occasion arises, you're looking at an investment of around one to two thousand dollars for one.
If you are looking for a raku kiln, then here are some kilns that you'll want to check out:
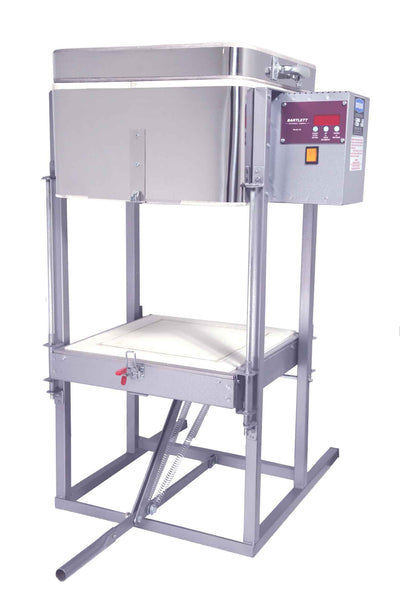
7. Ceramic/Glass Hybrid Kilns
The glass/ceramic kiln is a unique fusion that offers the benefits of two kilns rolled into one. In this intriguing design, most models incorporate heating elements both along the sides of the chamber, akin to ceramic kilns, and in the lid, resembling glass kilns. This ingenious arrangement empowers artisans to opt for the specific coils that best suit the requirements of their ongoing projects.
Undoubtedly, this remarkable versatility does come with a corresponding price tag. Investing in these kilns can range significantly, spanning from approximately $1000 to around $7500.
This dual-purpose kiln design not only caters to the multifaceted needs of artists who work with both glass and ceramics but also showcases the inventive strides that have been made in kiln technology. By merging the advantages of both glass and ceramic kilns, these hybrid models offer an exciting array of possibilities, giving creators more options and flexibility than ever before. It's important for individuals considering such a kiln to weigh the investment against their artistic needs and the range of projects they envision undertaking.
If you're looking for a hybrid kiln that can work on both ceramic and glass, here are some options we think you'll like:
Other Costs to Consider for Kilns
Beyond the kiln's purchase price, there are additional costs to factor in. This includes supplementary items such as kiln furniture, vents, rolling stands, and even electricians. Let’s take a look at all of these costs.
Kiln Furniture
Kiln furniture is tools and supports essential for firing items like pottery and metal components within furnaces. These elements are crafted from refractory materials since they can handle high temperatures without distorting.
Prices for kiln furniture are a wide range, starting at an average of around $30 for a basic shelf and a few posts to prices upwards of $1,000 or more. Premium kits often encompass not only multiple frames and posts but also supplementary items like protective gloves, cleaning equipment, and an assortment of posts tailored to different needs.
The final cost of a furniture kit hinges on several factors, primarily the number of shelves required, the quantity and types of posts needed, as well as the sizes and styles of shelves included. If you want to budget correctly, set aside $30 to $75 per shelf and around $4 to $8 per post. Taking into account the diverse assortment of options available, investing in the right furniture kit is a crucial step in ensuring the optimal functioning of your kiln and facilitating successful pottery firing endeavors.
Kiln Vents
There are two key options for vents: downdraft and updraft vents. The downdraft system efficiently removes fumes from the bottom of the kiln and expels them outside through a wall vent. On the other hand, the updraft system focuses on collecting gases located above the kiln and directing them out through a wall duct.
Beyond merely addressing unpleasant odors, these ventilation systems are crucial in creating a safer and more productive workspace. By minimizing exposure to harmful emissions, you're not only prioritizing your own well-being but also extending the operational life of your kiln.
The VentMaster is a great option for anybody who is looking for an efficient and well-designed downdraft vent.
Rolling Stands
Serving as crucial supports, rolling stands elevate kilns, maintaining a secure distance from the floor. Although many kilns come with their accompanying stands, sometimes you’ll need additional stands to help the kiln operate.
Some kiln stands are designed with casters or wheels, offering a distinct advantage for those who require frequent kiln mobility. These mobile stands are complemented by locking mechanisms that ensure stability and deter unintended movement. Notably, heavy-duty stands are a preferred choice for educators in elementary schools, a decision that augments stability, especially in settings where student access to kiln rooms is a factor.
Beyond their support function, kiln stands are engineered to endure the weight of kilns and the heat generated during firing. This heat resistance guarantees their longevity even through extended use. Moreover, kiln stands are available in various sizes, tailored to seamlessly align with a range of kiln dimensions. Whether you're a seasoned craftsman or an educator nurturing creativity, a well-chosen kiln stand is pivotal in establishing a secure, efficient, and adaptable workspace.
Electricians
Ensuring safety should be your top priority when considering the installation of a kiln, and that starts with having a qualified electrician thoroughly inspect your wiring beforehand.
You'll find a range of smaller kiln models in the market today, designed to operate on a standard single-phase, 20 amp, 120-volt household circuit. It's worth noting that these updated standards have been recently enforced, as it wasn't too long ago that the standard was 110-volt, 15-amp circuits.
To mitigate any potential safety risks and prevent any complications with your homeowner’s insurance, it's a prudent step to engage a licensed electrician to evaluate your wiring system.
In addition to these considerations, it's essential to bear in mind that the majority of kilns function on a 240-volt setup, and some models can draw a significant current of up to 60 amps. This necessitates the installation of specialized circuits capable of managing such a substantial electrical load.
Even if you're well-versed and skilled enough to undertake the task yourself, I'd strongly recommend against it unless you hold the credentials of a licensed electrician. The possibility of invalidating your home insurance coverage is a very real concern.
Remember, electricity demands respect and careful handling. Prioritize safety at all times when handling.
Conclusion
So, how much does a kiln cost? The answer is, it depends. Kilns vary in price based on what they’re used for, size, and supplementary items. For example, kilns that are used to fire pottery and ceramics have a different build than kilns electric kilns.
By understanding what you need to fire, you can identify what exactly you’ll need to take on your projects. From here, use our information above to find pricing and see if the kiln is in your budget. Happy firing and leave your questions in our comments below!
Try Our Kilnfrog Recommendations:
Leave a comment