What Can a Kiln Be Used For? 8 Uses
Kilns boast a long history, having been employed by different cultures for millennia. They can generate and maintain high temperatures, making them incredibly versatile tools. Think of a kiln as a close cousin to an oven; both serve the purpose of heating various objects. But what makes a kiln indispensable is its ability to reach and sustain the exact temperatures required to complete specific processes.
This allows kilns to be used in a number of ways for crafters, potters, and more. Today, we’ll look at eight uses you can utilize your kiln for. Let’s get started!
1. Heat Treatment / Knifemaking
Heat treatment improves a material's (typically metal) mechanical qualities such as strength, toughness, ductility, and wear resistance. It also enhances corrosion resistance and minimizes internal tension, making the material more robust and trustworthy. Heat treatment also makes it easier to shape materials into diverse shapes, such as castings, forgings, and extrusions, allowing them to fulfill design standards. This is typically done in a kiln, oven, or furnace with digitally controlled temperature monitoring. Typical heat streaming processes are; Annealing, Tempering, Quenching, and Normalizing.
Heat processing may be used on a wide range of materials such as metals, alloys, ceramics, glass, and polymers. * Gears, shafts, springs, and bearings in the manufacturing industry * Turbine blades, exhaust nozzles, and landing gear in the aerospace industry * Engine parts, brake discs, and suspension parts in the automotive industry * Surgical instruments and implants in the medical industry. for a more in-depth look at heat treating you'll want to check out the book, Practical Heat Treating: Basic Principles, by Jon L. Dossett
2. Enameling
An enameling kiln, typically a small front-loading unit, serves as a handy tool for testing colors or adding decorative touches to various materials like sheet metal tiles, functional ware, or jewelry. Enameling is the process of applying a durable and glossy colored glass coating that seamlessly bonds to the surface of the metal when heated in the kiln. This versatile technique works with materials like gold, fine silver, copper, steel, and even platinum. During firing, the enamel simply melts and melds with the surface, resulting in a beautiful and long-lasting finish.
3. Annealing for Blown Glass Pieces, Via Lampwork or Torchwork
Using your kiln for annealing blown glass pieces made in a furnace or with a flame is a fantastic creative pursuit. It can also be a delightful new hobby to explore. Glass blowing involves working with molten glass at extremely high temperatures and mastering the shaping skill. Whether you're interested in crafting small jewelry pieces or larger decorative items, this craft offers a wide range of possibilities. All this manipulation of the glass causes stress, which must be relieved in a process called annealing.
Glass expands when heated and compresses when cooled. These processes cause stress in the glass, notably between its inner core and exterior layer. To relieve these tensions, which can cause strain or break at normal temperatures, glass must be cooled through a precision temperature gradient. This is done through a process called annealing. Annealing cools glass controlled. The anneal soak, which equalizes glass temperature and relieves stress, is the first step in annealing. Annealing soaks range from 900ºF (482ºC) to 1080F (582ºC) depending on the type of glass being annealed. The glass thickness and kiln setup determine the soak time at this temperature. The purpose of annealing is to allow the entirety of the glass body to become temperature-uniform. Here’s a great glass behavior reference tool from Bullseye Glass Co.
4. Curing of Ceramics & Pottery
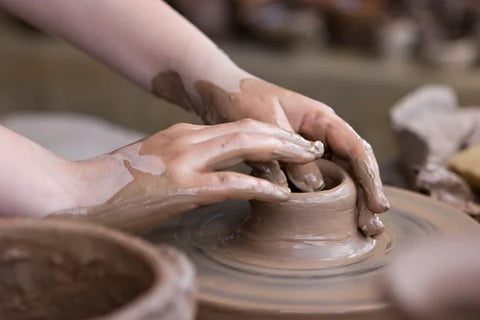
Pottery is made by firing clay or any ceramic substance using a heat source, often an electric or gas kiln at a predetermined temperature range, until the clay hardens. Ceramics, on the other hand, can be made by burning a variety of materials including clay. This makes ceramics useful in multiple industries, whereas pottery has more restricted applications. The firing range is governed by the type of ceramic clay/material used to manufacture the item. This makes selecting a versatile kiln for a new kiln buyer critical so that the maker can have a variety of creative experiences! For a full breakdown, check out our article on the best at-home kilns for pottery.
5. Drying
Using a kiln speeds up the drying process considerably. That's why most wood production mills opt for kilns to lower the moisture content of freshly cut lumber to the necessary level. The goal here is to maintain the moisture at a point where it won't cause any additional harm. Kiln-drying is especially essential in the furniture-making industry, helping to prevent common problems like warping and twisting in the lumber.
6. Fusing and Slumping Glass
Glass fusing and slumping methods heat glass in a kiln to make beautiful and useful glass items, but their goals and procedures differ. Glass fusing combines glass components into a single, layered composition, while glass slumping shapes the fused glass. Complex glass art creations with fused and slumped components sometimes combine these processes.
Glass fusing involves melting and fusing many pieces of glass into a single, solid item using heat. Layering colored or transparent glass on a flat surface or mold is customary.
For this, you'll need to choose some type of glass kiln. The following below are popular options:
Cress Kiln C1006B
After having been heated in a kiln, the glass melts and blends without losing its individuality.
By stacking and layering glass pieces, artists can create forms, patterns, and motifs during fusing. Glass fusing is used to make jewelry, plates, bowls, and elaborate glass art.
Glass slumping occurs after glass fusing. It involves placing fused glass in or above a kiln mold. When heated again at a lower temperature than fusing, the glass softens and collapses over the mold. Artists can add curves to flat fused glass or create three-dimensional objects.
7. Cement Making
The kiln is the most significant part of a cement factory since it performs most chemical reactions at high temperatures. A massive revolving steel kiln with a length-to-diameter ratio of 10–40 is utilized in rotary kilns. The modest slope and slow spin allow material movement long enough for thermal conversion. Counter-current kilns transmit heat more efficiently because gasses and particles move in opposite directions. The slope and rotation of the rotary kiln transport materials from the higher end to the lower and heated end. The lower end of the kiln burns the material which is then fired and dried and pyroprocessed to generate clinker. The red-hot clinker is ejected from the kiln and cooled via coolers.
8. Incinerators; ie Biomass
Kilns are thermally insulated chambers that serve as heating units for a variety of applications, including pyrolysis reactors. To ensure direct heat transfer to the biomass feed, the heat required for the reaction is directly generated inside the reactor itself in a kiln. Kilns are classified according to their shape and design. These large-scale kilns are very basic and simple to build. They are often built close to the biomass source to provide a constant supply of feed to the reactor. The existing biomass in a kiln transfers heat to the arriving feed.
Conclusion
To sum it up, kilns prove to be essential tools spanning numerous industries and crafts. They bridge the gap between traditional pottery and modern processes like incineration and heat treament. Kilns' exceptional capability to deliver precise and controlled heat is instrumental in crafting both functional and artistic objects.
Related kiln education content:
Explore our Top 3 Kilns:
Leave a comment