Ceramic Kilns: What buyers need to know
When you are looking for the perfect kiln, you might think there is one out there that does it all, but kilns are made for specific purposes. The perfect ceramic or pottery kiln might be a poor choice for an enamel artist. The best knife oven would not necessarily be great for a glass fuser. In the next few weeks, we are going to take a look at several different categories of kilns and discuss what we think are important features to look for when you are deciding on your next kiln. Let’s start with kilns for clay artists!
Firing Temperature
The first thing you should look for is firing temperature. First, we should point out that clay people use a measurement of heat called “cones”. For over 100 years, ceramic artists have used the pyramid shaped, ceramic pyrometric cones to measure heat in kilns. The cones are made from very carefully controlled clay compositions and they will bend at a specified temperature. We can thank Dr. Edward Orton Jr. for coming up with this very easy and accurate way to measure heat in the kiln environment. Of course, today we use digital controllers to keep track of the heat work in our kilns, but we still use the same cone ranges specified by Orton when referring to the various temperatures at which our clays and glazes reach maturity.
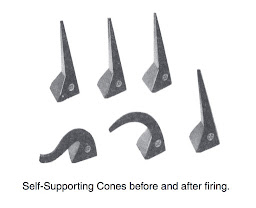
Low Fire – cone 09 to cone 1, or 1700º F to 2100º F. Low fire clays have the widest range of maturing temperatures, so knowing your preferred clay is important here.
Mid Fire – cone 5 to cone 6, or 2167º F to 2232º F.
High Fire – cone 8 to cone 10, or 2280º F to 2345º F.
Most ceramic kilns will either be rated to 2100ºF (cone 1), 2300ºF (cone 8), or 2350º F (cone 10), so choose a kiln that is right for your clay of choice. (If you’re not sure which clay you’re planning on using, err on the side of a cone 10 kiln. This will give you the most flexibility.)
Heat Source
Now that you have your firing temperature satisfied, be sure you have the right heat source. Ceramic kilns will almost always have side firing elements. If you are looking at a front-loading kiln, you might want to include door elements so that you get heat evenly distributed coming from all sides. Most smaller front-loading kilns do a really good job of heat distribution with only the elements in the three stationary walls, but the larger front-loaders really do benefit from door elements. Round or octagonal kilns benefit from the perfect, even heat distribution that clay needs for a good firing.
Power Supply
Make sure you have the right power supply for your kiln. This is always important, but since ceramic and pottery kilns usually fire pretty hot, you will most likely need to have a 240v power supply. Always consult your electrician to see what size breaker you need for the kiln that you have your heart set on. There are a few 120v ceramic kilns out there, but they are very small, and typically are used to test glazes, or for jewelry projects like beads and barrettes. To get a large volume of space up to ceramic firing temperature requires more juice, so you are going to want to be sure you have an adequate power source for the kiln that you purchase. A good way to think of this is more space=more power. 120v and 240v kilns will have different power cords according to the amperage rating of the kiln. Again, consult your electrician once you have your kiln selected to make sure that the circuit for your kiln is the correct voltage, has the proper receptacle, and has the correctly sized breaker for the amount of power the kiln is pulling. For very large kilns, you might need a direct wired connection.
You can find diagrams of the various outlet configurations here:
Top Loading vs Front Loading
Most ceramic and pottery kilns are round or octagonal in shape and load from the top. This is a very traditional design for ceramic kilns, but there is another option! A front-loading ceramic kiln makes getting larger pieces in and out of the kiln, especially in greenware, much easier! Front-loading ceramic kilns are typically larger and very well suited for the production ceramicist. Even if you are a hobbyist, the ergonomics of a front load kiln might be something you’d prefer. Round, deep kilns are harder on the back to load and unload, and if your height challenged this can be even more difficult. Plus, the wider the kiln, the heavier the lid can be, making it an even tougher job.
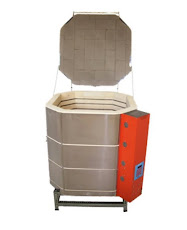
Kiln shape is another thing to consider when looking for a ceramic kiln. As I mentioned earlier, the traditional ceramic kiln is a round or octagonal shape that is tall enough for at least two or three layers of shelves. That being said, there are some great square top-loading and front-loading ceramic kilns out there. When you are considering what is the best fit for you it might be a good idea to lay out a typical load of your largest sized pieces and see what shape works best to utilize as much of your kiln space as possible.
To Vent or Not To Vent… what are the options?
Now we all know that kilns need to have adequate ventilation in their environment, but ceramic and pottery kilns also benefit greatly from interior ventilation systems. Usually referred to as a VentMaster, these internal vent systems give you many benefits in your firings:
- In the greenware to bisque stage, an internal vent system helps to get the excess moisture out of the kiln more quickly.
- During the glaze firing, internal vent systems get rid of excess moisture during the first portion of the firing, but also help your glazes to mature properly and develop more intense colors, especially in the red and yellow hues.
- If you are using glazes that have any toxic elements, this internal venting is essential to keeping your work environment safe. All of the noxious fumes inside the kiln are exhausted outside where they dissipate quickly and are not trapped inside with you!
Vent systems typically have a vent hole in the floor of the kiln where the vent attaches. The vent then pulls a small amount of air through the body of the kiln via a vacuum effect and then exhausts that air through an exhaust vent hose which you direct away and out of your firing area. This could be done through an exterior wall or through a series of hoses through a window, or out a doorway, or even into another wider, better-ventilated space.
Paragon and Olympic have the option of supplying a 240v Auxiliary Output Plug (AOP) on their controllers that will allow you to program when to turn your VentMaster on and off during your firing with the 12-key and smart touch controllers. In order to take advantage of this feature, you should specify the AOP option and the 240v VentMaster. Otherwise, the 120V VentMaster is simply plugged into a regular household outlet and turned on and off manually.
Size
And then there is size, and it does matter! Many people will tell you to buy the largest kiln you can afford, and there is a lot of wisdom in that train of thought. However, you don’t want to get a kiln that is so large that it takes you weeks to fill it up. That could get a bit frustrating if you are the type of person that loves to see results quickly. Of course, as you grow your skills as an artist, you might easily grow into a larger kiln. Speaking from personal experience, it takes a lot more planning to arrange work in a kiln when you work is 18-20 inches tall than when it was 6 or 7 inches tall. That’s where those half shelves that you see in the furniture kits come in handy! My last load of pottery had one half of my 22” tall kiln loaded with just two 18” vases on the bottom shelf, but the other side had three layers of shorter vases and bowls stacked up.
Location, Location, Location
Lastly, it is always good to keep in mind where you will put your new kiln when it arrives. Remember that ceramic and pottery kilns are usually reaching temperatures in the 2200-2350º F range and you should have a minimum of 12-18” of clearance from any combustible materials around your kiln. You should also have plenty of air circulation and ventilation in the space where you kiln will be located. It’s a great idea to have a portable fan that you can direct on your controller box to help keep it cool and happy.
Also, think about where you will store your shelving, posts, and other kiln furniture in the vicinity of the kiln. Make room for the essentials like your shelf primer too!
Hopefully this information will help in your decision making when considering a new ceramic or pottery kiln. If you need to talk things out, give us a call or shoot us an email. We are always happy to help you talk through your options and help you find the best fit for your needs.
Leave a comment